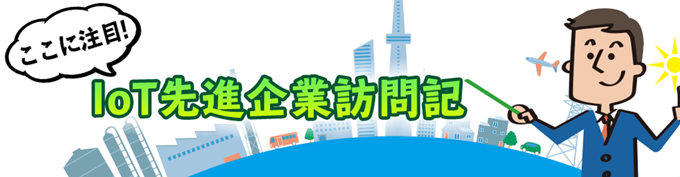
本メルマガは、IoT価値創造推進チームのリーダーである稲田修一が取材を行ったIoT導入事例の中から、特に参考となると感じた事業や取り組みを分かりやすくお伝えする見聞記です。
今回は、スカイディスク株式会社の取材を通して、過去の取材事例などからバックヤード変革に関する他の取り組みを振り返り、中堅・中小製造業の生き残りのための変革トレンドについてお伝えします。
【ここに注目!IoT先進企業訪問記 第79回】
スカイディスクの取材で確信したバックヤード変革の重要性
1. はじめに
「ものづくりを、もっとクリエイティブに」というミッションを掲げる株式会社スカイディスク(本社:福岡県福岡市)が提供している「最適ワークス」の取材を行った際に、製造業、それも中堅・中小製造業の生き残りには、生産計画立案におけるデジタル活用などのバックヤード変革注1が不可欠だと確信しました。この確信を形式知化するために、気付きを得たスカイディスク社のソリューション紹介とあわせて、過去の取材事例などからバックヤード変革に関する他の取り組みを振り返り、中堅・中小製造業の生き残りのための変革トレンドを探りたいと思います。
注1:ここでは、受発注管理、生産計画や原価管理、それを効率化する情報システムなどを担当している管理部門を「バックヤード」と呼んでいます。新商品の開発・製造などを担当し、直接的に売上げに貢献する部門との対比で使っています。この稿では言及しませんが、総務・経理などもバックヤードに含まれます。また、今あるものを新しいものに置き換える場合は「変革」という用語を、今あるものに変更を加え改善する場合は「改革」という用語を使っています。
2.スカイディスクの「最適ワークス」の概要
最適ワークスは、工場における生産計画のデジタル・トランスフォーメーションに有用な生産スケジューラです。「この製品を・何個・いつまでに」というオーダー情報から、設備・スタッフの最適な割り当て計画をAIが自動立案します。作成した生産計画をベースに進捗管理を行い、計画と実際の進捗の差分を分析することにより生産管理のPDCAサイクルを回すことができるようになります。
生産計画は、取引先の増加、生産品目数の増加、納期の短期化などにより複雑化しています。これまでのようなベテランの勘と経験では対応することが難しくなっており、独自開発の数理最適化AIを搭載した最適ワークスの出番が増えている状況だと考えられます。ちなみに、最適ワークスが作成する生産計画は、人が作成したものより7~10%程度効率的となるケースが多いそうです。このようなツールを導入した事業所とそうでない事業所では、生産性に差が出る可能性があり、それが生き残るか、淘汰されるかの命運を分けると感じたのです。もちろん、バックヤード変革の重要性も痛感しました。
最適ワークスの効用は、生産計画立案の効率化や精度向上だけにとどまりません。無理のない計画立案で残業が減った、納期遵守率があがった、不良品発生率が減少したなど、現場力の向上に直結する効用もあります。生産計画と実績の対比ができるようになり、イレギュラー対応履歴をもとにそれを改善するための部門間のコミュニケーションが活発化するなど、生産工程改善のためのPDCAサイクルが回りやすくなるなどの効用もあります。
しかしながら、最適ワークスの導入には、ハードルがあります。生産計画立案には、製品、工程、設備、生産能力、スタッフなど、様々な生産計画にまつわる情報とその関係性を、マスターデータとして整理し、紐付けて設定する必要があります。このマスターデータの設定には、製造におけるすべての要素や制約条件を洗い出すなど手間がかかる作業が必要なのです。幸いなことに、最適ワークスでは、この手間のかかる導入作業を効率的に行うツールがあり、ある導入企業では、通常は数か月以上かかる導入期間を最短で1か月に短縮しています。でも、そのような導入ハードルの高さを越えるメリットがあると判断する企業が多いようです。最適ワークスは2022年4月の正式リリース以降、2023年9月末の時点で累計100件超の導入が決まっています。
【参考】スカイディスクの「最適ワークス」の詳細
https://smartiot-forum.jp/iot-val-team/iot-case/skydisc
3.製造業の課題とバックヤード変革の役割
製造業は、構造改革の最中です。その本質は、中堅・中小事業所の淘汰です。生産性が改善すると、必要な事業所の数は減ります。海外との競争という要因もありますが、実際、事業所の数は、23.3万(2011年)から17.7万(2020年)へと10年間で24.2%減っています。一方、原材料使用額は179兆円(2011年)から184兆円(2020年)へと増加しています(図1参照)。また、全体の従業員数もコロナ禍で大きく減少するまでは増加傾向でした。限られたパイを奪い合う形で淘汰が進んでいると言えます。
中堅・中小製造業の方々に話を聞くと、取引先の増加、製造品目数の増加、短ライフサイクル化、値引き要求への対応などの課題解決が急務と指摘されます。このため、徐々にではありますが、IoTやAIなどのデジタル活用による製造工程の改革が進んでいます。
しかしながら、製造工程の改革だけでは、変革の時代を乗り切れないのではと感じます。巨大デジタル企業などの動向を見ていると、需要側とのインタラクションを含めたエコシステムを構築し、厳しい競争に対応していこうという大きな流れがあるからです。スカイディスクの取材の際に気付いたのは、製造業においてこのエコシステム構築に相当するものがバックヤード変革だということです。
ここでいう「バックヤード変革」とは、バックヤード業務をコストセンター的な位置づけから、需要側へのインタフェースとして直接的にプロフィットに関わる業務にかえることを指します。つまり、バックヤード業務をコスト削減のための「改善」としてとらえるのではなく、サプライチェーン全体や顧客、他社との商流に影響を与え、新たな価値を生み出す「変革」をもたらす活動としてとらえているのです。
最適ワークスを使うと、新たなオーダーがあった際にそれを受けることが可能なのか、いつまでに納入することが可能なのかについて、確度の高い回答を直ぐに需要側に返すことができます。このことで最適ワークスは、製造工程の稼働率向上という新たな価値を生み出す可能性があります。また、納期の短縮化要望に対応するために、どの工程を改善したら良いのかなどの立案も可能です。つまり、需要側とのインタラクションをリアルタイムに実現するエコシステム構築の第一歩となるサービスなのです。
このバックヤード変革に関しては、「最適ワークス」以外にもさまざまな挑戦が行われているので、その中のいくつかを紹介します。
4.バックヤード変革の例1:原価管理の自動化
需要側が大きな関心を持っているのは、納期や品質に加え価格です。この価格に直接関係するものづくりの原価管理をリアルタイムに、かつ、自動的に可能とするサービスがあります。株式会社KOSKA(本社:東京都千代田区)が提供する「GenKan」というサービスです。ちなみに、「GenKan」は、「Gen場とGen価をKan理する」を意味する名称です。
作業指示書にRFID注2付きのタグを貼って品番などを登録し、成形、曲げ、検査などの作業場所で作業指示書を決められた場所に置くと、タグの中身をRFIDリーダーが読み取り記録します。これで受注した製品に関する工程の進み具合を追跡します。一方、カメラで収集した情報から人が作業しているか否かなどをAIで判別し、各工程での実働時間などを収集します。RFIDとカメラという2つのセンサーでデータを自動収集し、このデータを生産管理や原価管理に活用するという、原理的には極めてシンプルなサービスです。(図2参照)
注2:Radio Frequency IDentifierの略語。電波の送受信によりICチップの中のデータを読み書きする技術のことをいいます。製品などの識別・管理に幅広く利用されています。
図2:「GenKan」サービスの概要(出所:KOSKA提供資料)
GenKanでは、工程ごとの作業時間を計測しています。これによって、多品種少量生産の場合であっても、個々の製品の労務費を把握することができます。製造原価を容易に、しかも、出荷する時点で把握することが可能となります。受注した製品ごとに見積もり原価と製造原価のズレを可視化し、そのズレを即座に是正することができるようになります。このズレの解消が赤字受注を減らし、収益性改善につながるのです。
また、受注した個々の製品の進捗状況を把握できます。製品納期に間に合うかどうかの確認や繁忙時に新たな受注を受けることが可能かどうかの判断も、容易にできるようになります。納期管理や今後の生産計画の策定が可能になるのです。このサービスも勘と経験に加え、実際の製造原価を把握した上での受注というエビデンスに基づく判断を助け、生産性向上や収支改善につなげるものです。また、同時に需要側とのエビデンスに基づくインタラクションを創出し、エコシステムの実現に貢献します。
【参考】KOSKAの「GenKan」の詳細
https://smartiot-forum.jp/iot-val-team/iot-case/case-koska
https://smartiot-forum.jp/iot-val-team/mailmagazine/mailmaga-20201126
5.バックヤード変革の例2:受注などのワンストップ化
従業員数120名の特殊鋼加工販売会社である深江特殊鋼株式会社(本社:広島県福山市)は、2020年に機械加工調達のためのウェブサイト「Meta-Navi」を開設しています。顧客が仕様、予算、納期を指定すると、同社のスタッフがZOOM会議で対応して条件を満たす業者を選定し、加工・生産管理・納品まで全てサポートするソリューションサイトです。(図3参照)
「受注」ではなく「調達」を使っているので、ビジネスの目線が需要者である顧客中心になっているのだと感じます。また、同社は全国300社以上の機械加工協力企業ネットワークを構築しており、顧客のさまざまな要望に対応できるようにしています。需要側とのインタラクションを実現し、さらにそれに対応する協力企業ネットワーク構築という一歩踏み込んだエコシステムを実現しています。
図3:Meta-Naviで実現させる機械加工の「ターゲット調達」
(出所:深江特殊鋼ホームページ)
このソリューションのポイントは、顧客が「納期」「価格」を伝えることで開始される「ターゲット調達」という顧客目線の新しい機械加工の調達方式です。顧客はワンストップで機械加工を依頼でき、注文を引き受けてくれる会社を探す手間が省けます。ウェブ上で創出した受注は全体の1割程度ということですが、販売エリアは全国に広がり、取り扱い商品数も確実に増加しているそうです。
このような仕組みを構築するメリットは、受注機会が広がることで工場の稼働率向上に貢献するだけでなく、商談データをデジタルデータとして蓄積することが可能になることです。需要側のニーズ変化を迅速に理解すると同時に、エビデンスに基づいた調達の相場観の理解にもつながります。良いものを作れば売れるという考え方は重要ですが、良いものの定義は時代によって変わります。勘と経験に加え、エビデンスによる顧客理解を深めることで、時代変化への対応を助けるのです。
このような顧客と生産者をつなぐ受注の仕組みを構築し、受発注・生産管理などをワンストップ化した例は、他にも衣服分野のシタテル株式会社(本社:熊本県熊本市中央区)、高難易度プレス金型製作の分野の株式会社ウチダ製作所(本社:愛知県知多市)などの例があります。
【参考】シタテルの詳細
https://smartiot-forum.jp/iot-val-team/iot-case/case-sitateru
https://smartiot-forum.jp/iot-val-team/mailmagazine/mailmaga-034-20191108
6.バックヤード変革の例3:工程管理の見える化
石川県加賀市の伝統工芸である山中漆器では、工程管理クラウドシステムを構築し、工程管理の見える化を実現しています。漆器生産は分業制です。漆器屋(問屋)がデザインを決めると、素地(きじ)屋が木地を挽き、下地工程を経て、塗師(ぬし)屋が下塗り、中塗り、上塗りと漆を塗り重ね、蒔絵屋が蒔絵を加えて完成します。
今までは、この受発注と進捗確認などの業務を電話とファックスに頼っていました。いちいち連絡しないと工程管理ができない状況は、効率が良くありません。これを改善するために、2017年に一般社団法人山中漆器コンソーシアムを設立し、バックヤード業務の効率化のために共同で工程管理クラウドシステムを開発したのです。(図4参照)
図4:山中漆器コンソーシアムによる工程管理の見える化の概要
(出所:山中漆器連合協同組合 竹中理事長の新潟県のDX協創プロジェクト全体会での講演資料「日本一の漆器産地 産地DXでイノベーション」を活用し、筆者作成)
これによって、「工程の見える化」と「受発注業務のデジタル化による支払・請求処理の効率化」を実現し、漆器屋1社当たり月平均で75時間の業務削減に成功しています。この業務削減で余裕時間ができたことは重要です。山中漆器では、新たにブランディング強化など若い世代へのアピールや世界市場への展開など、次の飛躍につながる新たな取り組みを促進しています。需要側とのインタラクションを含めたエコシステム構築に向けた取り組みを開始しているのです。
【参考】山中漆器の取り組みなどの詳細
https://smartiot-forum.jp/iot-val-team/iot-case/yamanakashikki
https://smartiot-forum.jp/iot-val-team/mailmagazine/mailmaga-20231201
7.バックヤード変革の実現に向けて
デジタル活用の進展により、中堅・中小企業においても設備稼働率の改善、不良品率の低減、検査の自動化など製造工程改革が少しずつ進展しています。工場のオペレーションは今までも数値化されており、改革効果が分かりやすいことがその要因の一つだろうと考えています。それに比べ、バックヤード変革は遅れています。業務全体の変革のイメージが描きにくいこと、変革効果を事前に数値化することが難しいことが大きな要因です。
しかしながら、生産計画・管理の複雑化に対応するため、何よりも需要側を含めたエコシステム構築を目指して、これからはバックヤードにおけるデジタル活用にも注力する必要があります。データ収集の粒度が細かくなり、また、大量のデータを処理し最適化する技術の進展により、バックヤードにおけるデジタル活用が可能となっています。需要側とのエコシステム構築という発想でバックヤード変革を進めることで、中堅・中小企業の競争力が向上し、我が国のものづくりを引き続き強力に支えていくことを期待したいと思います。
関連する事例紹介記事
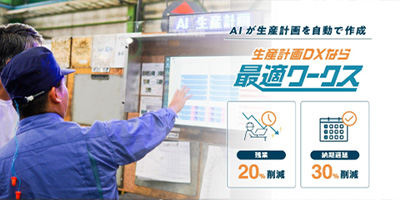
独自AIが生産計画立案を支援するサービス「最適ワークス」を活用し製造業の生産計画DXを推進するスカイディスク
製造業はオペレーションがまだまだアナログ的であり、自社の正確な生産能力が分からず、積極的な受注活動を控えるという事態が起きていた。受注を増やしたいのに受注機会を逃すという状況が、企業が成長する上で大きな阻害要因となっている。当社はこうした課題を改善するために、独自AI が生産計画立案を支援するサービス「最適ワークス」を正式リリースした。…続きを読む
IoT導入事例の募集について