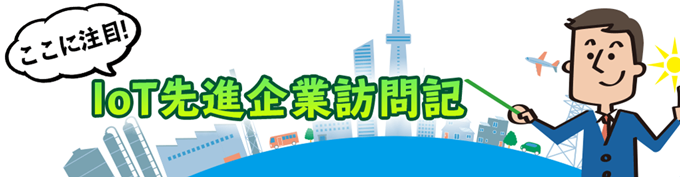
本メルマガは、IoT価値創造推進チームのリーダーである稲田修一が取材を行ったIoT導入事例の中から、特に参考となると感じた事業や取り組みを分かりやすくお伝えする見聞記です。
今回は、日本原価計算研究学会及びものづくりとITの融合をめざすIVI(Industrial Value Chain Initiative:インダストリアル・バリューチェーン・イニシアティブ)の共同研究がきっかけで生まれたベンチャー企業KOSKA(本社:東京都千代田区)のものづくりの原価管理自動化サービス「GenKan」を取り上げます。
【ここに注目!IoT先進企業訪問記(46)】
ものづくり現場での気付きから生まれたKOSKAの原価管理自動化サービス「GenKan」
1. はじめに
KOSKAの原価管理自動化サービス「GenKan」は、カメラやRFID注1などから収集したものづくりに関するIoTデータを活用し、生産状況の見える化と収益性改善につながる原価計算を自動化するサービスです。作業指示書にRFID付きのタグを貼って品番などを登録し、成形、曲げ、検査などの作業場所で作業指示書を決められた場所に置くと、タグの中身をRFIDリーダーが読み取り記録します。これで受注した製品に関する工程の進み具合を追跡します。一方、カメラで収集した情報から人が作業しているか否かなどをAIで判別し、各工程での実働時間などを収集します。
作業員にデータ入力などの負担をかけることなく、RFIDとカメラという2つのセンサーでデータを自動収集し、このデータを生産管理や原価管理に活用するという、原理的には極めてシンプルなサービスです(図1参照)。ちなみに、「GenKan」は、「Gen場とGen価をKan理する」を意味する名称です。
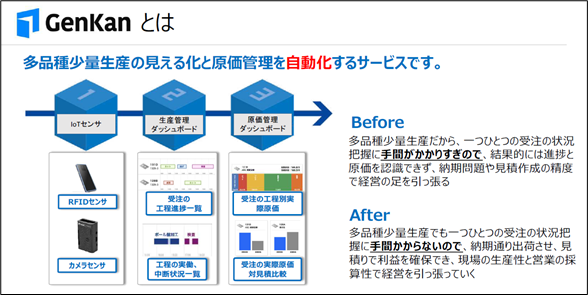
図1:「GenKan」サービスの概要(出所:KOSKA提供資料)
注1:Radio Frequency IDentifierの略語。電波の送受信によりICチップの中のデータを読み書きする技術のことをいう。製品などの識別・管理に幅広く利用されている。
2. サービスが生まれた背景
このサービスは、日本原価計算研究学会注2とIVI(Industrial Value Chain Initiative:インダストリアル・バリューチェーン・イニシアティブ)注3の共同研究がきっかけで生まれています。一橋大学在学中にこの共同研究に参画し、IoTを使って経営に役に立つデータを収集できるか否か、そのデータをものづくりの収益改善につなげる可視化や原価計算に使うことができるか否か、について2年間研究した現KOSKA代表取締役社長の曽根健一朗氏が、研究成果をベースにサービスを開発し、起業したのです。
GenKanは、原価計算のプロである曽根氏ならではの気付きがベースとなっており、それがサービスの骨格となっています。そして、いくつかの中小企業の協力で実証実験を積み重ねてサービスを改善し、中小企業の生産管理や原価管理の課題解決につながることを確信した上で起業しています。
注2:原価計算の理論および実践の研究を促進し、原価計算の進歩と発展に貢献するとともに、会員相互の交流を図ることを目的とした学会。
注3:ものづくりとITを融合することで生まれる製造業の新しいプラットフォーム構築に必要な共通基盤づくりを目的としているフォーラム。
3. サービス開発のきっかけは労務費が見えていないことへの気付き
製造業の方がまず気にするのは材料費です。最終製品を作る企業やその企業に直接部品などを卸しているTier1と呼ばれる一次請負の部品メーカーは大企業が多く、生産プロセスの自動化が進んでいます。したがって、製造原価の多くは材料費であり、労務費(製造に関わる人の人件費)の比重は高くありません。
これに対し、Tier1から発注を受けるTier2やTier3と呼ばれる二次請負や三次請負の部品メーカーでは事情が違っていました。研究を行っているうちに、材料費よりも人が関わる加工費の方が製造原価に対する影響度が大きいことが分かったのです注4。Tier2やTier3では中小企業の割合が高くなり、そこでは人が機械を動かす工程がかなりの部分を占めています。人の役割が大きく、今までのIoTが重視していなかった労務費の見える化が重要だったのです。これが最初の気付きでした。
このため、GenKanは人の現場作業に関わるデータを収集し、生産状況の見える化や原価計算を行っています。部材の破損や不良品の発生率など部材費に関わるデータや生産設備の改善・改良につながる詳細データなど、製造分野における多くのIoTが力を入れて収集・分析しているデータは使っていません。このことが、シンプルではあるが中小企業の経営から見ると有用なサービスの実現につながったのです。
注4:会計学における製造原価は、材料費、労務費、経費(製造間接費、減価償却費など)からなる。製造原価から材料費を除いたものは、加工費と呼ばれている。
4. データ収集は現場に負担をかけないことが基本
ものづくりの現場で労務費の見える化を行うのは、容易ではありません。今までは、作業員が作業実績を日報に記録し管理部門がそれを集計する、作業の開始時と終了時にデータを入力しそれを集計する、あるいは第三者がストップウォッチで作業時間を測定するなどの方法でこれを計測していました。データの収集に手間とコストがかかり、これが大きな課題でした。
これに対し、GenKanは、この課題をRFIDやカメラを利用することで解決しました。一見誰でも思いつきそうなアイデアですが、作業員の動きをきめ細かく観察し、現場に負担をかけない解決策となっています。しかも、現場導入の際に課題となるコストについても、さまざまな工夫で低廉化に成功しています。
実際、実証実験においてストップウォッチで計測した作業実績のデータとGenKanで計測したデータを比べて、「こんなに違うのか」と驚かれたそうです。ストップウォッチでは、通常、1時間ほど計測しますが、計測中は作業者が熱心に作業を行い良いデータとなる場合が多いのです。通常の作業実績とは異なるデータを収集する危険性があるのです。
それに対し、GenKanでは、RFIDやカメラなどのセンサー設備を設置すると、作業中ずっと計測することができます。これにより、作業にしばしば中断が生じていることや昼過ぎにはパフォーマンスが悪くなる時間帯があるなど、実際の作業実績を計測することができます。また、作業員の違いによる作業ムラを検出することも可能です。(図2参照)
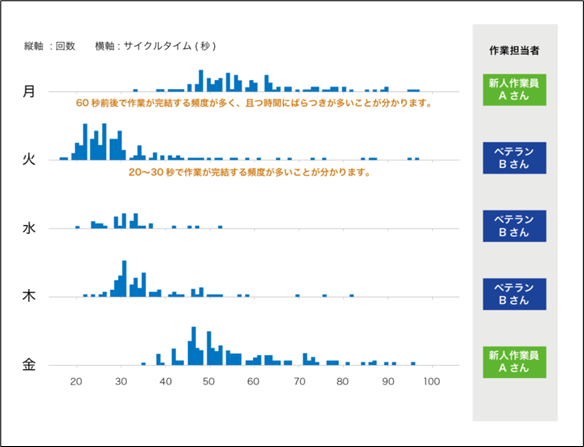
図2:曜日別の工程作業のヒストグラム分析(出所:KOSKAホームページ)
※月曜と金曜は複数の工程を掛け持ちしている新人作業員が作業を担当しているため、作業速度が遅く、大きなムラが発生しています。火曜から木曜はベテラン作業員が担当しているので作業速度は比較的早くなっていますが、曜日でムラがあること、一日の中でもサイクルタイムが長くなる場合があることが分かります。
5. 多品種少量生産の効率化に使えるという発見
サービス開発において、もう一つの大きな気付きは新たな活用分野の発見です。サービスを開発する中で、GenKanが量産だけでなく多品種少量生産の効率化にも有効であることに気付いたのです。もちろん、量産と多品種少量生産では、データの活用方法が異なります。
量産の場合は、一つの工程のデータを長期間に渡り収集し、原価変動の状況を明らかにすることが基本です。そして、これが価値の源泉となります。原価変動の原因を特定し工程を改善することにより、原価を下げ原価率の悪化を食い止めることができるからです。また、作業方法の改善などによって、原価が下がったかどうかを確認できることも重要です。
一方、多品種少量生産の場合は、同じ工程でも製品が変わると作業方法が異なります。一つの工程のデータを長期間に渡り収集しても、それだけでは価値に結びつきません。また、企業が抱えている課題も量産の場合とは異なります。製品ごとに作業時間が異なり、かつ、一製品あたりのロット数が少ないので、そもそも製造原価の見積もりが難しく、さらに実際の製造原価についても算出できないことが課題だったのです。
GenKanでは工程ごとの作業時間を計測しているので、個々の製品の労務費を把握することが可能で、製造原価を容易に把握することができます。しかも、出荷する時点で製造原価が分かります。受注した製品ごとに見積もり原価と製造原価のズレを可視化し、そのズレを即座に是正することができるのです。このズレの解消が赤字受注を減らし、収益性の改善につながります。既存のIoTでは解決が難しかった課題を解決できたのです。
また、受注した個々の製品の進捗状況が把握できます。製品納期に間に合うかどうかの確認や繁忙時に新たな受注を受けることが可能かどうかの判断も、容易にできるようになります。納期管理や今後の生産計画の策定が可能になるのです。まさに、「勘・経験・根性」に加えて、実際の原価というエビデンスに基づく経営判断を可能とし、これが生産性向上や収支改善につながるのです。
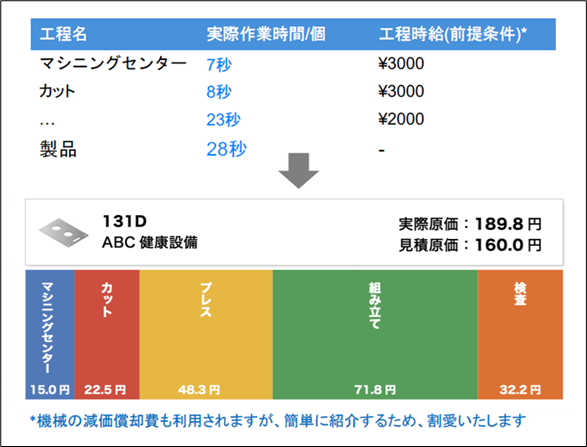
図3:GenKanによる原価計算のイメージ(出所:KOSKA提供資料)
6. 今後の期待と展望
Tier2やTier3の企業が日本でものづくりを続けることの意義は、多品種少量生産における品質の高さです。これは現場が工夫を積み重ね、作業方法を常に改善していること、それに作業者の質が高いことに起因しています。この現場の強みが、働き手の急激な減少やコロナ禍による外国人労働者の減少で危機に直面しています。
GenKanは、人不足に悩む工場経営者がその解消のために自動化をどの工程から進めると効果的なのか、そしてそれが原価削減につながるのか否かを明らかにできます。また、その導入によって現在の人員で生産を継続することが可能かどうかの見極めも可能にします。このサービスは、製造原価の可視化を通し、現場のエビデンスに基づく合理的な経営判断をサポートする有用なツールなのです。
ものづくり現場にもGenKanは効用をもたらします。現場の個々の工夫がどれくらいの製造原価削減につながったのかを明らかにできるので、これが現場での工夫を促進し、さらなる削減に貢献します。また、作業者にほとんど手間をとらせることなく導入可能なので、海外でも活用は容易です。
GenKanは、2020年10月の時点で既に20社以上の利用実績があり、自動車・電気部品から金属や樹脂、食品の加工・生産業など幅広い分野で使われています。同社は、専門のデータコンサルタントがデータの分析を行い、ものづくりの改善について顧客企業と議論しています。このコンサルティングを通じて、多品種少量生産の分野で生産性や収益性のさらなる改善に必要なさまざまな知見やノウハウを集積しており、この集積が同社の競争力の源泉となるのです。
このサービスの採用がさらに広がり、それが我が国のものづくりの一層の強化につながること、同社が知見やノウハウのさらなる集積に成功し、ものづくり分野のデータ活用企業として大きく飛躍すること、この両方を期待したいと思います。
今回紹介した事例
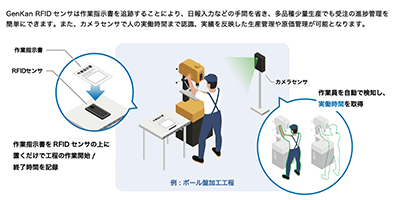
IoTで原価を見える化し現場と経営をつなぐ − 株式会社KOSKAのGenKan
製造業において、原価を正しく把握することは経営の根幹である。中小企業では労務費が原価の最大要素となっているが、工程作業時間の正確な把握にはコストや作業者の負担が増えるなど、収集が困難であった。これを解決するために、IoTを活用して作業者への負担なく作業時間を収集し、工程の原価として自動的に見える化するサービスGenKanを開発した。…続きを読む
IoT導入事例の募集について