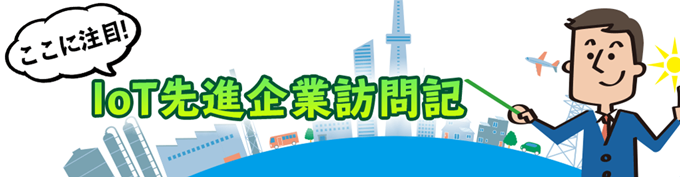
本メルマガは、IoT価値創造推進チームのリーダーである稲田修一が取材を行ったIoT導入事例の中から、特に参考となると感じた事業や取り組みを分かりやすくお伝えする見聞記です。今回は、貫流ボイラの最大手で国内シェア50%を超える三浦工業(本社:愛媛県松山市)の予防保全を取り上げます。
【ここに注目!IoT先進企業訪問記(18)】
IoT導入のパイオニアに学ぶ-三浦工業のオンラインメンテナンス
三浦工業がIoTを導入し、ボイラのオンラインメンテナンスを始めたのは1989年にさかのぼります。今から29年前のことです。故障に結びつく異常をデータ分析で割り出し、故障前に調整や部品交換する予防保全を実施しています。歴史が長く、かつ、大きな成功を収めている同社の取り組みから学べることは多々あります。IoT導入のパイオニアである同社の取り組みをご紹介しましょう。
1. 高い利益率を誇るメンテナンス事業
三浦工業のメンテナンス事業は、会社の屋台骨を支える事業に成長しています。同社の2018年3月期の売上高は1249億円、税引前利益は142億円(国際会計基準による)ですが、売上の27.8%、利益については実に59.0%がメンテナンス事業によるものです(図1参照)。メンテナンス事業は景気の波に左右されにくい特性を持っていますが、その事業の利益率がコンスタントに20%程度を維持し、高収益に大きく貢献しているのです(図2参照)。
顧客が同社に支払うメンテナンス料金の額は、業界の相場を考えると決して高い水準ではないそうです。同社の高収益体質はIoTを活用し、小さな改善を積み重ね、事業運営を効率化した結果として実現したものなのです。
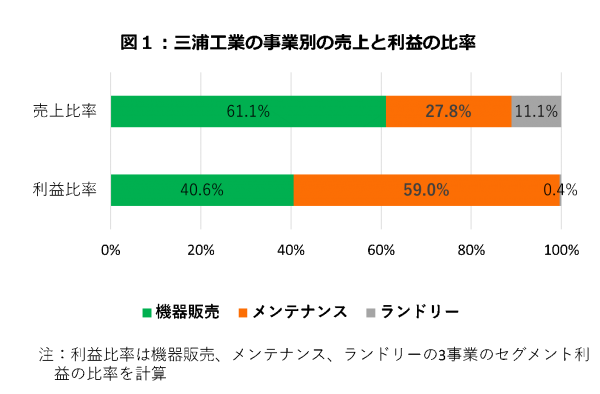
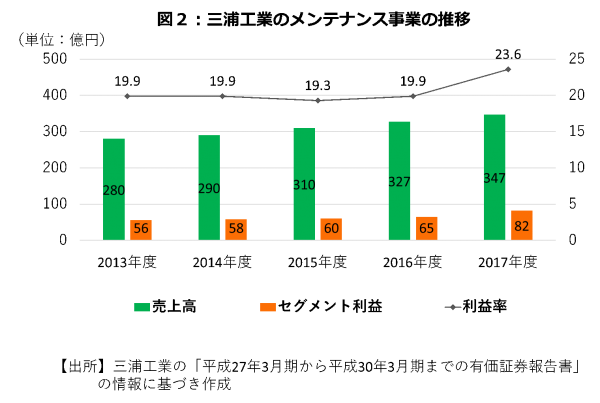
2.創業者の強い想いから始まった予防保全で離職率も低減
三浦工業が、ボイラのメンテナンス事業に力を入れ始めたのは1972年です。創業者の三浦 保氏が北米のエレベータのリモート監視に啓発され、保守契約プログラム付きでボイラ設備の販売を始めたのです。営業や販売店からは、「他社メーカーに価格で負ける」「メンテナンス料金は、修理完了後に請求するのが当たり前だ、前金ではもらえない」と強い抵抗があったそうですが、「メンテナンスは故障の前に行うべき!」という氏の強い想いでこれらの抵抗を押し切り開始しています。
同社の会社案内には「ミウラの歴史は、改革と挑戦の連続です」と書かれていますが、まさに、今から50年近く前にまだ世間に定着していなかった予防保全の考え方をボイラに導入したのです。さらに、ボイラ設備から収集したデータを活用すれば、より有効な予防保全が可能になるのではないかと考え、1989年にはオンラインメンテナンスを開始しています。当時はまだインターネットが普及していない時代ですので、アナログモデムを利用し、通信容量の不足は、自己判断機能付きのマイコンを活用することで補いました。
このような先進的な予防保全の考え方は、顧客にもすんなりと受け入れられた訳ではありません。営業や販売店が顧客の理解を得るため地道な努力を積み重ねるうちに、「こわれない」「とまらない」「省エネ運転できる」価値が徐々に理解されるようになったのです。現在では、大半の顧客が保守契約プログラム付きでボイラを購入し、遠隔監視するボイラなどの機器は約6万台を数えます(2018年4月現在)。また、更改の際に、大半の顧客が他社の製品に乗り換えず、同社の製品を選ぶ状態になっています。そして今では、メンテナンス事業が同社のビジネスを利益面からしっかりと支える形になっているのです。
オンラインメンテナンスの導入は、働き方改革にも大いに貢献しています。導入前はメンテナンス要員の離職率が高かったそうです。何故なら、ボイラが止まると顧客が多大な損害を被るケースが多いため、夜間・休日に関係なく故障修理の緊急対応が必要で、メンテナンス要員は1年365日24時間体制でこの対応に追われたからです。しかし導入後は、次第にこの状況が改善しました。故障予知の精度があがり、計画的なメンテナンスを実施することで緊急対応が激減したからです。現在は、約1,000名いるメンテナンス要員が夜間・休日に緊急出動する頻度は平均して月150件、受信件数の1%未満になっているそうです。
3.データ活用の効用を高めた継続的な改善と人材育成
現在でこそ高効率・高精度を実現している同社のデータ活用ですが、導入当初から効果を上げていた訳ではありません。初めは故障予知の精度が低く、異常の前段階であることを警告する「お知らせデータ」に基づいて出動しても「空振り」が多かったそうです。この精度を高めたのはデータ収集項目の見直しや判定ロジックの見直しなど、地道な改善努力を継続したことです。
データ収集項目に関しては、例えば、監視対象をボイラ本体だけでなく給水や電源など関連するユーティリティ部分に拡大しています。水処理設備のトラブルによってボイラに負担がかかりトラブルの原因になりますが、従来はボイラ本体に異常が現れるまで検知することができませんでした。監視対象を給水部分に拡大することにより、ボイラ用水の変化や劣化を検知し、ボイラ本体のトラブルにつながる発生原因をなくすことで故障なく運転できるように改善したのです。
一方、判定ロジックに関しては、例えば、「お知らせデータ」を出すスケールの厚さを見直し、0.3mmに設定しています。スケールとは、ボイラ水に含まれるカルシウム・マグネシウムなどが、熱交換を行う配管内に付着してつくる硬い皮膜のことです。この付着は、ボイラの熱効率を悪くなるだけでなく、配管の温度が高くなり故障につながるので、事前保守の重要な判断要素となっているのです。
しかし、このような地道な取り組みを行っても、さまざまな要素が複雑に絡み合うケースをすべて網羅できるものではありません。このような場合、判定精度の向上は、収集したさまざまなデータを見て最終的に判断する人の能力に依存します。メンテナンスの基本は「人」なのです。三浦工業のすごいところは、収集したデータを分析し、ワンストップでトラブルを解決できる総合的知識・スキルを持ち、顧客ごとに最適な保守計画を策定することができるサービスエンジニアの育成が必須だと認識し、これを育成する社内教育制度と社内機種資格制度を創設し、これを積極的に活用していることです。これらの制度を通して生まれたスキルの高いエンジニアの存在が、データ活用の効用を高めているのです。
さらに同社は収集したデータをメンテナンスの改善に使うだけでなく、商品品質の向上や新商品開発にも活用しています。これは、トラブルそのものの減少にもつながります。例えば、異物混入による給水の逆流がとまらなくなるトラブルが多いことをデータから発見し、これを防止する弁を技術開発し、このトラブルを激減させています。
このように小さな改善や改良を積み重ね、また、これを実施する人材を組織的に育成することで、メンテナンス事業の効率を少しずつ高めていったのです。
4. 新しい技術への挑戦が今後の課題
このように大きな成功を収めている三浦工業の予防保全ですが、さらなる高度化に向けていくつかの課題が出てきています。その一つは、今までの成功体験からの脱皮です。同社のIoT活用では、IoT向けの新しい通信システムの導入、クラウド活用や機械学習導入などが必要となっています。同社はオンラインメンテナンスで大きな成功を収めているだけに、新しいツールの導入には高いハードルが待っていると想定されます。従来のやり方で大きな効果を実現しているので、新しいツールを導入しても今まで以上の成果をあげることが簡単ではないからです。しかし、グローバル市場で成功を収めるためには、最新技術の利用は避けては通れない課題です。
同社のボイラは多品種少量生産の典型で、一機種当たりのデータ量は多くはありません。一般に多くのデータを必要とする機械学習や深層学習を活用するには、適切な適用領域の発見や少量データに向いた手法の採用などの工夫が必要となります。例えば、適用領域に関しては、メンテナンス作業の一層の効率化を図る、より正確な判断を支援するなどの活用が考えられるでしょう。また、単にデータ分析に頼るだけでなく、故障に至るまでのパターンを人工的に再現し、これに関する詳細なデータ収集を行い、知見を得ることが有効な場合もあります。要は、新しいツールの出現により、これらの活用を含めた最適なメンテナンスのやり方を再検討する時期に来ているのです。
しかし、この場合も基本となるのは最先端のツールを使いこなし、データを読み解く「人」となります。同社が新しいツールに対応できる人材育成を推進し、ボイラ分野のIoT活用に新しい可能性を切り拓くことを期待したいと思います。
|
|
1989年に業界に先駆けリモートセンシングによる予防保全を実現した - 三浦工業「オンラインメンテナンス」 「故障の連絡を受けてから、現場に駆けつけるのでは遅い。ボイラは生産に直結する」「未然に損害を防ぐ保守点検を行うべきだ」、という創業者の強い思いから営業・販売店の強い抵抗を押し切り、トップダウンでスタートした。...続きを読む |
|
IoT導入事例の募集について