IoT導入のきっかけ、背景
当社は、主にボイラの製造販売・メンテナンスを事業とするグローバル企業である。ボイラは、工場の生産を支える重要なインフラであり、その信頼性を最大限発揮できるように運用するためには、日々の運転状態の確認と定期メンテナンスが重要である。そのため当社は、製品の販売がゴールではなく、そこからがスタートと考え、保守契約プログラムZMP®(Zボイラ メンテナンス プログラム)を1972年に導入した。このプログラムをさらに進め、1989年にオンラインメンテナンス®を開始し、トラブルが発生する前に事前に解決ができる、データに基づく予防保全を確立した。
当社のZMPは、創業者の、「故障の連絡を受けてから、現場に駆けつけるのでは遅い。ボイラは生産に直結する」、「生産を止めるとお客様が多大な損害を被る。未然に損害を防ぐために、保守点検を行うべきだ」、という強い思いから営業・販売店の強い抵抗を押し切り、トップダウンでスタートした。
ZMPプログラムを進める中で、予防保全をシステム化することができると、この契約がよりよいものになると考えた。予防保全に関しては、従来も保守マニュアルを整備し、運転時間などを基に定期的な点検や部品の交換を行っていたが、さらに、機器から収集した多くのデータを加えることによって、機器の運転状態・負荷状態等に基づく、お客様毎にカスタマイズした点検整備が可能となった。
このデータを取得するために、インターネットがまだ商用化されていない1989年の時点で、ボイラにマイコンと通信機能をいち早く搭載し、機器の遠隔監視を実現した。
また、監視はボイラ本体だけではなく、給水や電源など、関連するユーティリティ部分との境界点にも適用している。従来は、トラブル発生の連絡を受け、サービスエンジニアが現場で調査を行うと、ボイラ本体ではなくユーティリティ部分がトラブルの原因であることが少なからず存在した。遠隔監視を導入することによって、このような場合も、トラブルの切り分けを遠隔で行い、当社保守拠点からお客様にユーティリティ部分の復旧をお願いすることにより、現場まで出向せず、いち早くトラブルを解決できるようになった。
2018年4月現在、約6万台(ボイラ以外の機器も含む)の機器でオンラインメンテナンスをご利用いただいており、当社製品を導入いただいたお客様の多くに、本サービスのメリットをご理解いただいている。
IoT事例の概要
サービス名等、関連URL、主な導入企業名
サービスやビジネスモデルの概要
本サービスでは、製品購入時に、ZMP契約をあわせてご購入していただく(オンラインメンテナンスはこの中に含まれる)。ZMP契約の期間は3年で、契約満了時に、最大4回の契約更新が可能となっている。これによって、お客様は最大15年間(*)の設備稼働期間を通じて、定期点検や保証範囲内の部品の交換サポートを受けることができる。
(*): 運用開始から最初の12年間(4契約期間)がフルサポート期間。残り3年間は延長サポート期間となる
オンラインメンテナンスによる予防保全を行うことによって、突発的な故障の発生率を大きく低減した。これによって、夜間・休日にサービスエンジニアが緊急出動する回数も大幅に低減した。また、本サービスによるメンテナンスの革新を他社に先駆けて実現したことによって、サービスの売り上げによる安定したキャッシュフローの実現に加え、サポート期間終了後の機器リプレースの際に、改めて当社の製品を選定いただく高いリピート率を達成し、お客様との好循環を生むことができた。
内容詳細
オンラインメンテナンスに対応したボイラには、マイコンと各種センサ群が搭載されており、マイコンがボイラの運転状態を常時監視する。マイコンが異常を検知した際は、以下の2種類のアラーム情報に分類し、当社の地域メンテナンス拠点および本社のZISオンラインセンターに通知する。
- お知らせデータ:重故障につながる可能性があり、予防保全が必要な事象
- 重故障:機器の停止または性能の著しい低下などを伴う故障
即時対処を要する異常が発生した際は、以下の対応を行う。
- 発生時間が平日昼間帯の場合は、最寄りのメンテナンス拠点がデータを確認し、必要な復旧措置をお客様に依頼する
- お客様にて復旧ができない場合は、サービスエンジニアが出向し対応を行う。その際に、お客様が使用している機種とアラーム情報から、必要な交換部品をピックアップした上で出向する
- 夜間休日時間帯は、本社のZISオンラインセンターが対応し、必要に応じてサービスエンジニアの出向を指示する
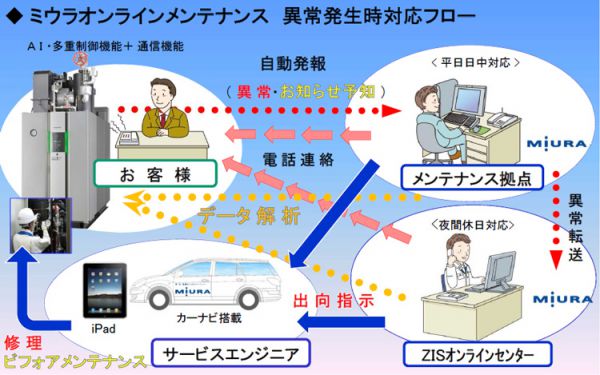
即時対応が不要なお知らせデータは、以下の図に示す通り、定期点検の際に行うべき交換部品の特定等に使用する。これによって、故障が発生する前の予防保全を効率的に実現している。
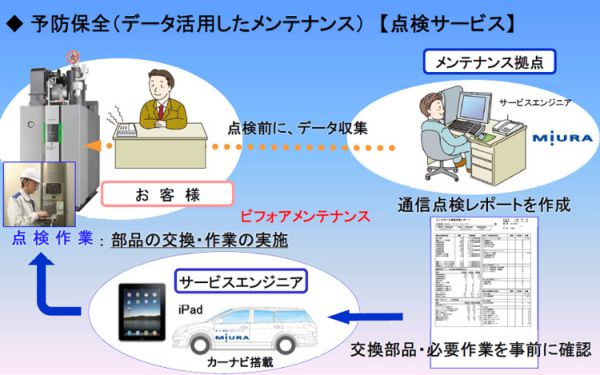
加えて、収集した運転情報(蒸発量、燃料使用量など)を基に、お客様毎にカスタマイズした、ボイラの省エネ運転に関するご提案や月報の提供を行っている。
概要図
オンラインメンテナンスシステムの概要を以下の図に示す。
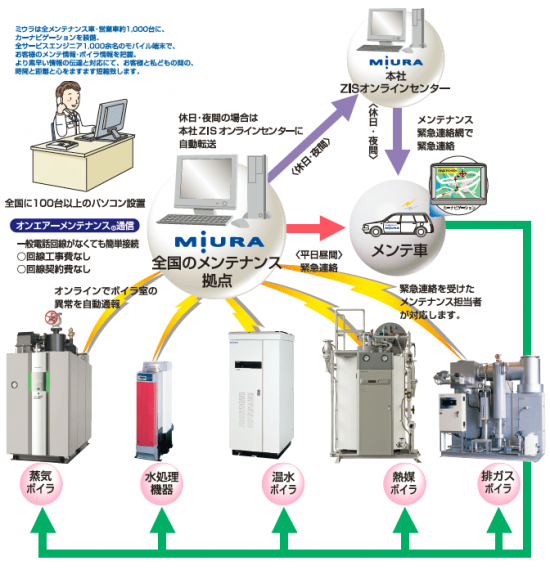
取り扱うデータの概要とその活用法
オンラインメンテナンスで収集しているデータは以下の通りである。
- 着火回数などの運転頻度
- 燃焼温度などの運転状態
- 各種センサの閾値越え情報
- スケール(水垢)付着・煤付着などの効率低下を監視するデータ
上記の情報を総合的に評価することによって、予防保全の計画を策定する。加えて、アラーム種別毎の発生回数を社内ビックデータとして蓄積し、メンテナンスの改善、製品の改善や新商品開発に活用している。
事業化への道のり
苦労した点、解決したハードル、導入にかかった期間
収集したデータを分析し、適切な保守計画を策定できるサービスエンジニアの育成が必要であった。その際に当社は、ボイラ単体に加えて、給水や電力という関連ユーティリティ部分にも精通し、ワンストップでトラブルを解決できる総合的知識・スキルを有するエンジニアの育成を目標とした。そのために必要な教育マテリアルの充実に加えて、資格認定制度を作ることにより、今では、国内に1000名を超えるエンジニアを擁している。
導入初期は、お知らせ情報が発生しても、その後の故障につながらないケースが散見された。そのため、重要な故障の予兆を見逃すことなく、かつ不要なアラームの発生を抑止するために、アラーム発生閾値等をチューニングする必要があった。
技術開発を必要とした事項または利活用・参考としたもの
リモートメンテナンスを行うことによって、故障や異常発生の要因を見える化でき、具体的な対策(製品の改善)を行えるようになった。例えば、異物混入による給水の逆流が止まらない異常が多く発見された際には、逆流防止弁を新たに開発する等の製品改善につながった。
今後の展開
現在抱えている課題、将来的に想定する課題
お客様の通信回線確保の容易性を加味して、一部の機種では、ボイラとオンラインセンター間の通信手段として電話回線(アナログモデム)を使用しているが、アナログモデムが次第に生産終了となっている。そのため、アナログモデムを内製に切り替えている。
強化していきたいポイント、将来に向けて考えられる行動
将来的には、その他のM2M用モバイルデータ通信を使用するなど、通信手段の置き換えを検討している。また、収集したデータを機械学習・AIで処理することによる、予兆監視精度の向上を検討している。その他、クラウド活用やセキュリティ強化などについても対応が必要になっている。
将来的に展開を検討したい分野、業種
オンラインメンテナンスは中国、韓国などアジア各国や北米、中南米でもでも既にサービスを開始している。本サービスの対象国をさらに拡大したい。