
株式会社KMC
- コスト削減
- 事業・業務プロセスの改善
- 故障や異常への迅速な措置
【活用対象】
- 自社の複数部門あるいは全体で活用
IoT導入のきっかけ、背景
現在、世界のものづくりは、電子情報の活用が競争力の決め手となる時代を迎えている。そのキーワードになるのは「データ」。しかしながら、製造業の現場はさまざまな生産機械が存在しており、これらをネットワーク化し新しい仕組みを構築するまでにどうしても時間がかかる。この促進に必要なのは、日本のものづくりを熟知した専門家による的確な技術コンサルティングと現場にぴったりと寄り添った形で製造業のイノベーションを支援する「日本版IoT/M2Mシステム」の開発・提供ではないかと考えた。
このシステムでは、電子情報の活用を前提としていない古い生産機械への対応や現場作業時の操作の容易性など現場ニーズを踏まえた機能を実現した。これによって、中小企業様から大企業様までの幅広い製造業のイノベーションを支援している。
ここで事例を紹介するA社様(自動車部品メーカ)は、企業変革の一環として設計プロセスや生産マネジメントの改革を積極的に進めておられる。これを実現する一環として、当社(KMC)のシステムを導入されたもの。
IoT事例の概要
サービスやビジネスモデルの概要
当社のIoT/M2Mビジネスは、技術コンサルティングの実施、「日本版IoT/M2Mシステム」を構成する電子カルテ、∑軍師などの開発・提供がメインである。また、導入企業はさまざまな規模の製造業となっている。ここで紹介するのは、A社様が構築された同じ失敗を2度と繰り返さない仕組みとそれを実現するシステム構築の事例である。
内容詳細
KMCの「日本版IoT/M2Mシステム」は、大きく3つの分野に分けられる。工場内の生産機械をネットワーク接続し、稼働状況を見える化する「M2M製品群(Σ軍師、QR銘板など)」、職人のナレッジ、各製造プロセスにおける生産状況などの膨大なデータをクラウド上で保管する「IoT製品群(電子カルテ(M-Karte)など)」、そしてクラウド上のデータを知識・管理指標化するとともにノウハウを可視化することで経営者や現場が最大限活用することを支援する「AIM※製品群(M-Documentなど)」である。
※ AIM: Artificial Intelligence Management
その3分野の中心に位置するのが、開発・製造経験豊富なKMCの精鋭チームが提供する「スマートエンジニアリング」である。技術コンサルティングから、人材育成まで、お客様の現状を詳細に分析し、最適な打ち手を提案している。
A社様は、当社の「ナレッジ電承」シリーズを導入され、開発や設計に関わるあらゆるノウハウをデータベースに蓄積して共有できる仕組みを構築されました。金型トライ時の情報収集や情報共有には金型電子カルテを導入し、現場情報を設計や生産技術にフィードバックする仕組みも実現されました。
ナレッジ電承:生産や生産技術に関する技術資料を集約し、さらに熟練設計者のノウハウを漏らさず記録する「足跡を残す機能」を盛り込んだツール。長年培ってきた経験値やノウハウを継承し、共有・資産化できる。
電子カルテ:金型や生産機械、作業者などをQRコードで管理、不具合事象を声・画像・動画でリアルタイムに把握することにより、生産現場のトレーサビリティ確保を可能にする。
概要図
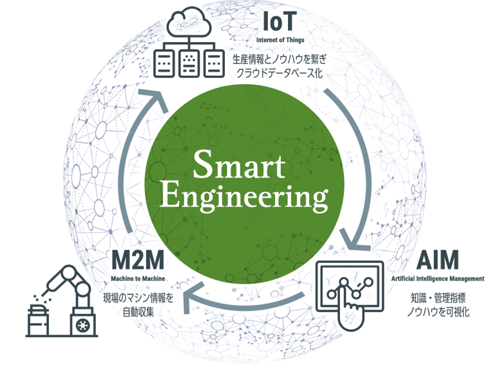
取り扱うデータの概要とその活用法
- ナレッジ電承では、生産技術情報、特に金型成立性、量産性等のノウハウ情報を扱っている。
- 金型電子カルテでは、樹脂成形トライ時の不具合情報および後工程の不良情報を収集している。
- これらの情報は、タブレットにより記録され、不具合分析やノウハウ分析等に活用されている。また、ナレッジの共有・維持・進化の為のリサイクル(PDCA)にも活用されている。設計と現場をデータで繋ぐという試みは過去にもあったが、リアルタイム性が確保できないこと、ノウハウ情報更新に人手がかかるなどの理由でうまくいっていない。今回の試みは、IoTというリアルタイムの情報収集手段とナレッジ電承という設計支援システムを連携させることにより、この課題をクリアした。
事業化への道のり
苦労した点、解決したハードル、導入にかかった期間
苦労したのは、投資対効果の試算である。対応工数を含め詳細なデータが無かったため、概算での費用算出になった。しかしながら、A社様の決断で、日常の作業に追われ放っておかれることが多い失敗事例を現場の負担なくリアルタイムに入力可能なシステムを構築し、同じ失敗を繰り返さないために不可欠な失敗事例のデータベースを実現できた。システム構築には半年程度かかったが、実際に運用が始まると、目に見える投資対効果が出始めた。
取組みの中で感じたことは、リアルタイムなコミュニケーションの効力。設計・生産技術を担当する部署と生産を担当する部署は会社が異なり、そのノウハウの融合に従来から取り組んではいたが、どうしても人対人の属人的なコミュニケーションが融合のベースであり、個人差等が生じがちだった。今回、ナレッジ電承(設計・生産技術情報)というシステムと電子カルテ(現場情報)を有機的に連携させる仕組みを完成させたことにより、コミュニケーションが抜本的に改善された。この部分は、ノウハウの標準化など含め3年計画で取り組み、実現している。
技術開発を必要とした事項または利活用・参考としたもの
金型製造要件を標準化し、設計に反映させることにより、過去の同じ失敗を2度と繰り返さない仕組みの構築、そのためのシステム構築が大きな技術課題であった。この技術課題を解決するため、過去の製品設計・生産技術・金型要件等を標準化することが必要であった。このため、A社様とKMCとで合同プロジェクトを発足させ、技術コンサルティングを実施しながら標準化作業を進めた。システムとしては「ナレッジ電承」シリーズを導入し、開発や設計に関わるあらゆるノウハウをデータベースに蓄積して共有できる仕組みを開発した。金型トライ時の情報収集や情報共有のために金型電子カルテを導入し、現場情報からの設計・生産技術へ情報をフィードバックするシステムも開発した。
今後の展開
現在抱えている課題
今後、国内の設計、生産技術、製造拠点だけでなく、海外の生産拠点やサプライヤーへの展開が課題となる。また、海外生産拠点とのデータ交換、国内拠点と海外拠点との間でのリアルタイム情報共有も課題となる。ソフトウエアベンダーのKMCは、海外サポート体制強化と販売・サポート拠点の現地法人を設立して対応を始めている。
強化していきたいポイント、将来に向けて考えられる行動
サプライヤー含めた生産活動の変化に対応し、簡単な対応で追随することができるIoT/M2Mシステムの開発が重要である。
連携を含めた強化分野
IoT/M2Mシステムとしては、上位のERP※やMES※とのシステム連携を視野に国内外の他企業とのシステム連携を模索している。M2Mについても、生産加工機や周辺機器、センサー等の開発スピードが速くなっており、関連メーカとの情報連携が益々必要になっている。