IoT導入のきっかけ、背景
半導体製造において、直径300mmのシリコンウエハーを用いた新規工場では生産の自動化が進んでいるが、200mm以下のウエハーを使用する既存工場では、製造装置への製品の投入や取出し等人手による作業が数多く残っている。一方で、グローバルな競争に勝ち抜くためには、既存の生産設備や作業員等のリソースを活用しながら、効率化を行う必要がある。
製造は、ヒト(作業員)、モノ(製品)、セツビ(製造装置)の3大要素から成り立つが、当社は、工場内における製品位置の可視化、製造装置の稼働状況可視化を既に行っており、モノとセツビの領域では既に生産の効率化を実現している。残る「ヒト」の稼働効率改善は、3大要素の中でも重要なファクターであり、その対応が急務であった。ヒトの効率化のために作業の自動化を行うことが考えられるが、現状の問題点を十分洗い出さず拙速に実行してしまうと、既存プロセスの非効率な部分を含めて自動化してしまう可能性があり、期待する費用対効果が得られない。そのため、今回は自動化を対象とせず、以下のステップで既存プロセスの課題抽出を徹底的に行った。
- 現状見えていない作業者1人1人の位置を、ビーコンによる屋内測位によってリアルタイムモニター
- 作業者の動線(移動履歴)と作業項目の関連性を可視化し、無駄がないかを分析
上記のデータ収集と分析から、熟練作業者と非熟練作業者間で移動距離が大きく異なることが分った。これが生産性向上の阻害要因になっていたのである。
そこで、このような移動距離の違いが発生している原因を分析し、非熟練作業者でも熟練作業者並みの効率で作業を行えるように改善を進めている。これによって、現時点で約10%の作業効率化が見込まれ、かつ、将来的にも生産性向上に大きく寄与することが期待されている。
IoT事例の概要
サービス名等、関連URL、主な導入企業名
サービス名(ツール名称):M3 Vision Monitor
3つのM・・・Man&Material&Machine(ヒト・モノ・セツビ)
3つのVision・・・リアルタイムモニター・先見改善・No1工場を目指す夢
サービスやビジネスモデルの概要
M3 Vison Monitorは、屋内測位技術による作業者のリアルタイムモニター及び作業者稼働率算出・分析の自動化を実現するシステムである。
(協力会社:マルティスープ株式会社、提供アプリケーション:iField INDOOR)
内容詳細
シリコンウエハー上に微細加工を行う半導体製造は、パターン形成、エッチング、酸化・拡散などの多くの製造工程に分割されている。当社の工場では、製造工程毎にクリーンルームが設置されており、工程内の処理に必要な製造装置と作業工程を管理する端末(着工PC)が設置されている。
各工程では、到着した製品を着工PCの指示に従って製造装置に投入し、処理が終了した製品を次工程に送る作業を行う。ここで、製品の種類が数百以上と多いこと、品種によって処理を行う製造装置が異なること、通常ロットに加えて優先ロット(少量の試作品等)が混在することから、オペレーションは単純作業の繰り返しではない。そのため、作業者がどのように動いているかを知ることがヒトの作業を効率化する上で重要である。
M3 Vision Monitorでは、各作業員に貸与したスマートフォンが、受信したビーコンのIDを測位サーバーに送信することによって作業者の位置測位を行い、動線をリアルタイムにモニターする。
図-1は、あるクリーンルーム内での作業に伴う動線を可視化したものであるが、熟練作業者Bさんと、非熟練作業者Dさんでは移動量が大きく異なることが分る。Dさんは、一つの作業が終る毎に着工PCと製造装置間を行き来しており移動量が多い。一方でBさんは、これまでの経験から次に行うべき作業を理解して行動しているため、最初の作業完了後に、着工PCに戻ることなく次の作業を開始しており、移動距離が少なくなっている。
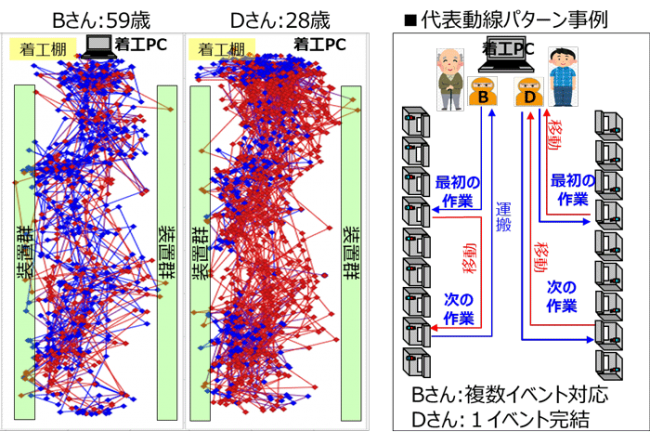
次に、作業員の移動と処理ロット数の関係を分析した結果を図-2に示す。一日当たりの処理ロット数を見るとDさんが最も多い(156ロット/日)ため、一見Dさんのパフォーマンスが最も高いように見える。しかし、ロット当たりの移動距離に着目すると、Bさんが39.1mと最も少なく、一方でDさんは59.0mと最も長くなっている。
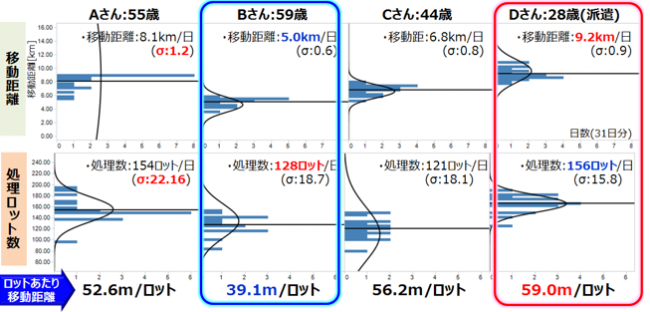
生産性として理想的なのは、Dさんが移動の無駄を減らし、Bさんと同レベルのロットあたり移動距離を達成することである。そうすれば9.2kmを移動できる体力を考えると、現在の処理数156ロット/日を235ロット/日に増やすことが可能になる(処理数:9200/39.1 ≒ 235ロット/日)。そこで改善施策として、熟練者の動きを蓄積し効率的な動きを蓄積されたデータから導き出し、「Dさんのスマートフォンに次に行くべき製造装置を指示することによって、Bさん並みの最短移動による作業」を目指している。また同時に、M3 Vision Monitorによって作業者の位置を常時把握しているので、最も移動効率がよい作業者に直接指示を送ることで移動の無駄を減らしている。
多くの工場と同様に当社の工場でも高齢化が進んでおり(平均年齢47歳)、将来的には退職に伴う人員の入れ替えや派遣社員による補充が必要となる。その際に新規雇用者は、Dさんと同様のパフォーマンスとなり、従来のやり方では既存従業員との間で生産性のバラツキが生じてしまうところを、このシステムを使用することによってバラつきがない高効率ラインが実現できる。
さらに将来的には、工場全体の稼働平準化を目指している。現状は、クリーンルーム単位で最適化を行っているが、クリーンルームによっては人員の不足により、製造装置の人待ちが発生している場合がある。その際に、モニター結果を活用し、人員に余力があるクリーンルームから応援を出すことによって、人待ちを解消することができる。
概要図
製造は、ヒト、モノ、セツビの3大要素が複雑に絡み合って動いており、ヒトの効率化を行うためには、各々を密に連携する必要がある。そのため、M3 Vison Monitorでは、図-3に示す通り、各要素をレイヤーとして管理し、レイヤー間の連携を行っている。
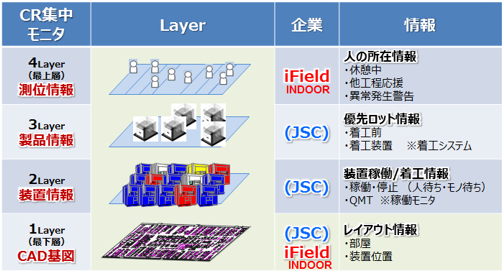
例えば、第3レイヤーでは優先ロットの所在地を管理しており、第2レイヤーの装置稼働状況と連携することによって、最短工程で処理できる製造装置を特定できる。次に、第4レイヤーのヒトの位置情報と連携することによって、製造装置に最も近い作業者に指示を送ることができる。次に、作業者が製品を製造装置に投入して着工処理(処理の開始)を行うと、第2・3レイヤーの情報が更新される。また作業を行った際に、作業者のIDと使用した装置やロットが紐付けられ、ロット当たりの移動量など生産性を計測するためのデータを生成する。
このように、4レイヤーを重ねて情報を集約することによって、ヒト、モノ、セツビの密な連携を実現している。
取り扱うデータの概要とその活用法
M3 Vison Monitorで扱う主なデータは以下の通りである。
- 作業者の位置情報(ビーコン信号による屋内測位から取得)
- 製品ロットの所在地情報
- 製造装置の稼働情報
導入に当たり苦労した点、解決したハードル、導入にかかった期間
工場内には大型の製造装置など、電波を遮蔽する障害物が存在する。M3 Vision Monitorでは、作業者のスマートフォン近傍に存在する3カ所のビーコン信号を受信することによって測位を行っているが、実証実験開始当初は、ビーコン信号のRSSI(信号強度)の揺らぎによって測位精度が安定しないことがあった。そのため、ビーコンの設置間隔、場所、電波強度を調整し、測位精度を検証する実証実験を複数回行う必要があった。
位置測位精度を維持するためには使用するスマートフォンの機種検証が必須であるが、安価なスマートフォンは製品寿命が短い。そのため、初期検証に使用したスマートフォンは検証終了時には生産終了となってしまい、新機種での再検証が必要となった。
技術開発を必要とした事項または利活用・参考としたもの
位置測位情報の収集と装置稼働情報システム・MES(Manufacturing Execution System)を連結し、作業者の行動を推測する技術、加えて、前後の行動を組み合わせることで行動測位精度を向上する技術を開発した。協力会社(マルティスープ株式会社)と共同で分析ツールを開発した。
今後の展開
現在抱えている課題、将来的に想定する課題
人の見える化イコール「監視」という負のイメージを持つ作業者も多く、労働意欲、モチベーション低下を招かないために、管理者より導入目的を伝え理解してもらう必要があった。
自動化に関しては、RPA(ロボティック・プロセス・オートメーション)の導入企業も多くなっており、当社も一部検証を開始しているが導入には課題があると考えている。RPAによって自身が必要とされなくなるのではという作業者の懸念から、作業者とのコミュニケーションが十分に取れず、RPA導入に必要な現状業務の課題(負荷やリスク、経験則による業務)が十分に特定できない可能性があるためである。
また、業務が効率化(省人化)された際には、従来の人材は高負荷価値業務へのシフトが必要だが、年齢的な問題もあり厳しく、そういう方々の活用について熟考が必要である。
強化していきたいポイント、将来に向けて考えられる行動
現在は、熟練者の動きの分析結果、それに製品と作業者の位置情報から、最も移動効率が高い作業指示を出すようにしているが、熟練作業者のノウハウを体系化し、指示決定アルゴリズムに組み込むことによって、作業者間のバラツキをさらに低減したい。
屋外の施設(動力・工水)の管理、点検等へ拡大を行いたい。屋外施設の点検は項目が多いため、点検の効率化が期待できる。また、作業を1名で行うため、転倒の検出など、安全対策としての活用も考えている。
将来的に展開を検討したい分野、業種
今後、以下の展開や検討を行いたい。
- グループ内の他拠点展開
- スマートフォンに変わるデバイスの検討(製造終了対応)
- 半導体製造装置はダスト付着の検査など製造品質に関わる保全作業が重要である。そのため、装置保全者への展開を行いたい(動作含めた分析)
本記事へのお問い合わせ先
株式会社 ジャパンセミコンダクター