IoT導入のきっかけ、背景
当社は、富山県を拠点としたスイッチング電源(直流安定化電源)を主力製品とする電子機器メーカーである。スイッチング電源は電子回路を安定動作させるための重要部品であり、当社の製品は小型・軽量・高効率であることから、情報通信機器や医療用機器、FA(Factory Automation)機器等を始めとして、様々な電子機器に使用されている。
当社における製造の特徴は、多品種少量生産である。製品の種別は、実に19,000種類に及ぶ。この多品種少量生産を効率的に行うために、当社はセル生産方式(*1)を採用しており、約130の生産ライン(セル)を有する。
コーセルは長年「人を中心としたセル生産方式」を基盤に改善活動を継続的に実施し生産能力向上を実現してきたが、昨今の慢性的労働力不足、懸念される高齢化社会、また、今後の急激な市場変化にも対応していくために、抜本的な生産プロセス革新が求められていた。
そこで、当社の生産ラインで広く使われ、また品質に大きく寄与する重要工程である「はんだ付け工程」に焦点を当て、従来の装置に代わる新たなはんだ付け装置を新規開発した。開発に当たっては、はんだ付けの品質を向上させるのはもちろんであるが、それに加え品質に大きく寄与する重要パラメータのデータをリアルタイムに収集できる装置にすることをめざした。従来の装置は、人の勘と経験による管理であったが、これをデータによる管理に変えたかったのである。そのため、はんだ付けの品質を左右する、フラックス(*2)塗布量の制御、はんだ槽内の温度管理などを、IoTの手法を取り入れてデジタル化し、データによって管理する方式に改めた。その結果、はんだ不良の発生率を90%低減するという、当初の目標を大きく上回る成果を達成した。
(*1):少数の作業者チームで製品の組み立て工程から完成までを行う生産方式。従来のコンベアライン方式は大量生産向けであるが、セル生産方式は多品種少量生産に適している
(*2):はんだ付けで接合する金属表面の異物や酸化膜を溶かし、はんだ付けを促進する薬剤
IoT事例の概要
導入事例の概要
当社が製造するスイッチング電源ユニット(写真-1を参照)では、回路基板(写真-2を参照)を貫通するスルーホールに部品のリードを挿入し、スルーホール内に溶融したはんだ(錫の合金)を浸透させることによってはんだ付けを行う。これによって、部品を基板上の回路パターンに接続する。
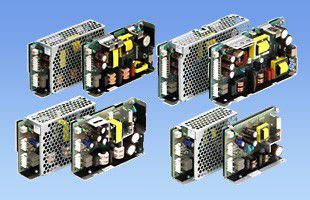
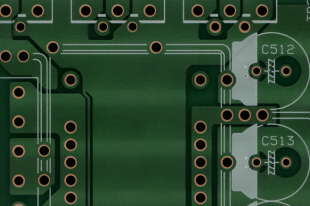
はんだ付け工程では、はんだ装置内のはんだ槽に溶融したはんだを満たし、槽内に送り込まれた基板をはんだ槽に浮かすことによって、スルーホール内にはんだを浸透させる。この工程ではんだ付けの品質を左右する要素は以下の2点である。
- 基板が溶融はんだに接触した際の加熱によるフラックスのガス発生量を、フラックスの役割を維持しつつ最小限にすること。このためには、はんだ付け前に行うフラックスの塗布量を最適化する必要がある。
- 基板が溶融はんだに接触する際のロバスト性を考慮し、主要条件のばらつきを最小限にすること。このためには、はんだ付け時にはんだ槽内温度を均一に保ちながら、はんだ温度管理を最適化する必要がある。また、環境への影響を考慮し、基板が溶融はんだに接触した際に生じるはんだ槽内の温度低下を、はんだ付け品質が確保できる最小限の熱量にする必要がある。
上記を実現するためには、既存のはんだ付け装置の改良では不十分と判断し、新はんだ付け装置を自社で開発した。開発では、フラックスの塗布量や基板が溶融はんだに接触する際の主要条件の最適値などを求めるために、設定条件を変えた実験を繰り返し、はんだ付け品質との相関データを積み重ねた。即ち、データの収集と分析によって最適制御を実現した。
内容詳細
今回開発した新はんだ装置によって得られた成果を以下に示す。
開発で得られた膨大なデータの蓄積によって、はんだ槽内温度など装置内でセンシングしている監視パラメータと、ヒータなどの制御パラメータの相関関係が得られ、リアルタイムにフィードバック制御を行っている。また、制御パラメータが最適な範囲を逸脱した際には、稼働監視システムに異常を表示すると共に、各種データの相関関係から、異常個所を作業員に示すことができるようになった。
新はんだ付け装置では、装置の運用コストも大きく削減することができた。具体的には、図-3, 4に示す通り、はんだ・IPA(溶剤)費用を48%削減、メンテナンス作業工数を60%削減、設備電力使用量の63%削減を達成した。
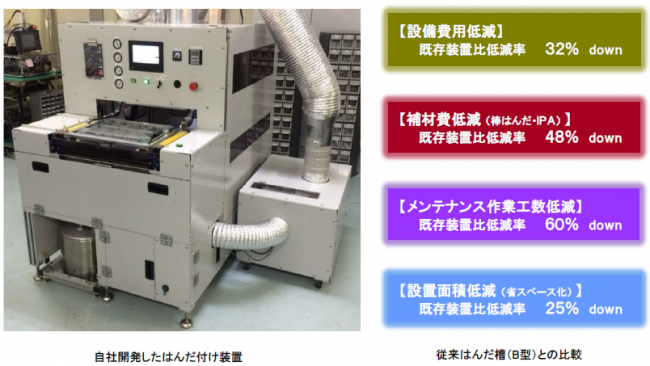
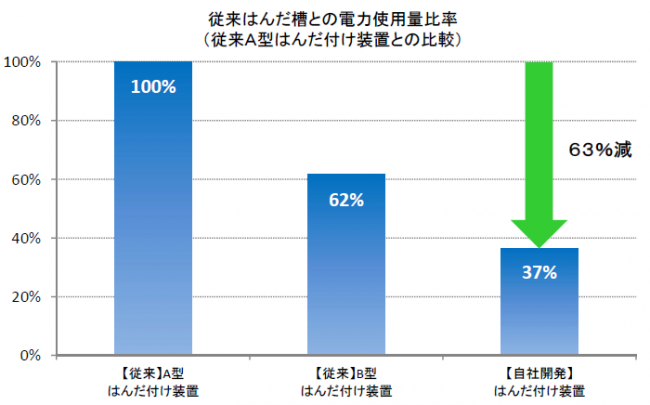
セル生産方式の改革 ― フレキシブルな人と設備の共存ラインの構築
新はんだ装置の開発に加えて、IoTを活用した生産方法の革新として、更なる「フレキシブルな人と設備の共存ライン」の構築を今後実現していく。この取り組みの一つとして、生産量の増加に応じて人を柔軟に投入できる生産体制をめざしている。当社工場では、通常時はセル当たり2人の作業員で生産を行うが、受注が増加した際は3名体制とすることによって増産を可能としている。これを工場全体で最適化を図るために、IoTに対応した設備からの稼働状態を収集し生産管理システムと連携することで実現していく。
また当社は、協力会社に設備と材料を提供し、生産量の約70%を外部に委託している。そこで、協力会社の主要設備を当社の稼働監視システムに接続することによってマザー工場による一括管理を行い、効率的に設備の保全品質を維持することにより製品品質を実現している(図-5を参照)。今後は、協力会社との生産量調整を効率的に行える仕組みも構築していく。
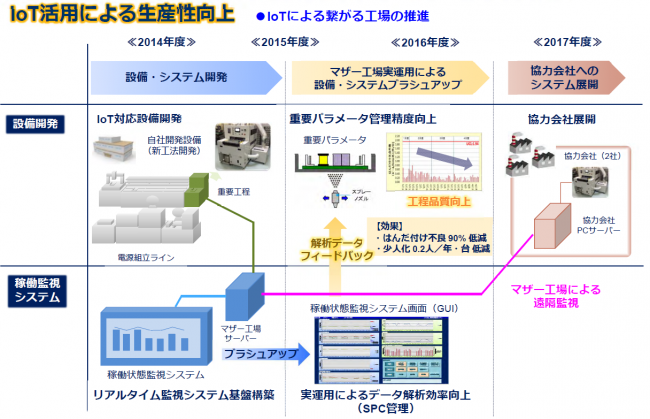
取り扱うデータの概要とその活用法
新はんだ装置では、以下のデータを常時収集して生産品質の監視と改善に向けたフィードバックを行っている。
- はんだ槽内温度・はんだ付け時間・はんだ槽への製品浸漬深さ、等
- フラックスの流量・粒子径、等
事業化への道のり
苦労した点、解決したハードル、導入にかかった期間
本プロジェクトにおいて、要求品質を満たす要素技術開発のみでなく、現場に新たなシステムがスムーズに浸透する運用システムの検討を重視した。調査していく中で抽出された多くの制約条件に対し、各課題の本質を見極め妥協しない全体最適視点での検討を繰り返し行ったことで実現に繋がった。
技術開発を必要とした事項または利活用・参考としたもの
-
はんだ付け工法(プリヒートレスフローはんだ付け・セパレート式キャリア)
-
品質に関わる重要パラメータを監視する稼働監視システム
今後の展開
現在抱えている課題、将来的に想定する課題
人の役割は更に高付加価値を生む作業にシフトしていくことを考慮し、「フレキシブルな人と設備の共存ライン」を今後も追求していく中で、単純作業の自働化だけでなく高難易度作業の自動化を効率良く実現していくことが課題である。
強化していきたいポイント、将来に向けて考えられる行動
組立ラインから取得した生産進捗データを生産管理システムとリアルタイムに連動させることで、お客様の要求納期にフレキシブルに対応できる生産体制を今後構築していく。
将来的に展開を(他企業との連携を含め)検討したい分野、業種
はんだ付けの品質検査に関して、画像認識技術に統計的学習機能を付加させることにより、フローはんだ付け分野における確度の高い自働化を実現し、本はんだ付け装置とのリアルタイムフィードバック制御システムの構築を検討する。